USB-3 Continuous Bitumen Modification Unit (12 m3/hour)
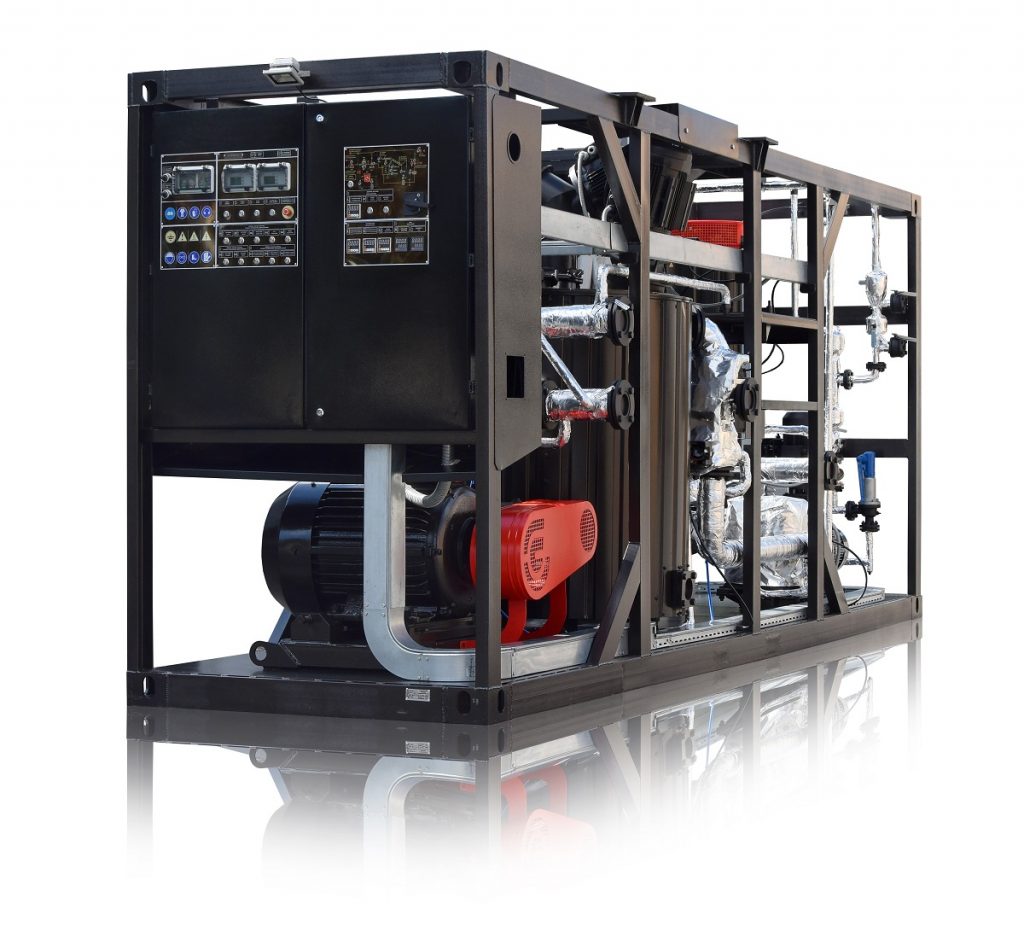
The USB-3 unit is engineered for the continuous production of modified bitumen, boasting a rated capacity of 12 cubic meters per hour.
In the modification process, the USB-3 unit accommodates various modifiers available today, including crumb rubber, special additives, and SBS-polymers in granular, powdered, or liquid form. This versatility extends to facilitating the implementation of new formulations involving adhesion additives and plasticizers.
Optional components that can be integrated into the unit include a sulphur feeder, polyphosphoric acid feeder, Big-bag monorail hoist, weighing batcher, compressor, and a mill with a mechanical seal and support system.
Operating Principle
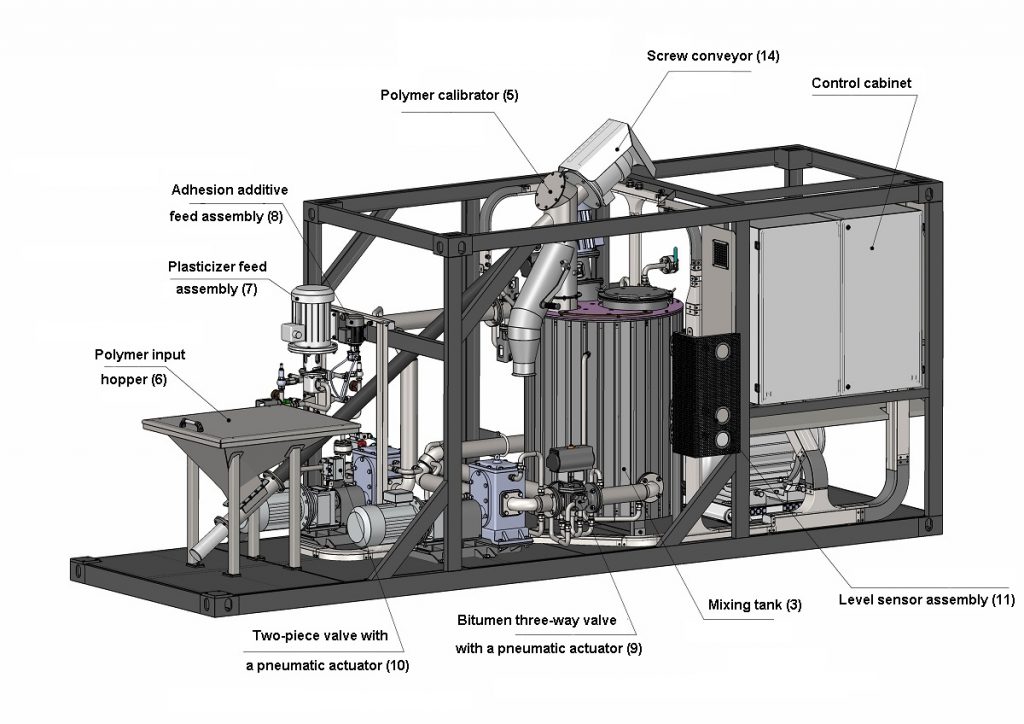
- Polymer is introduced into the hopper.
- The operator sets the formulation for polymer-modified bitumen on the control cabinet.
- The unit is activated.
- Bitumen and polymer are metered into the intermediate tank.
- Liquid additives are pre-fed into the bitumen.
- A high-speed mixer inside the tank preliminarily blends polymer and bitumen.
- A gear pump transfers the mixture to the mill for grinding and homogenization.
- Upon completion, the unit automatically flushes with clean bitumen to prevent blockages.
- The unit is then ready for subsequent operation.
Technical Features
- Installed within a spatial structure suitable for transportation in a standard 20-foot container.
- Equipped with a high-speed colloid mill featuring cutters designed for efficient grinding, cutting, and homogenizing of polymer-containing bitumen.
- Cutters with a symmetrical profile, doubling their service life with a change in rotation direction.
- Pumping equipment includes a frequency converter to regulate the supply of premixed bitumen and polymer to the mill, optimizing homogenization.
- Polymer batching system incorporates a hopper with a spiral conveyor, controlled by a frequency controller, ensuring precise polymer-to-bitumen ratio.
- Intermediate tank facilitates thorough mixing of bitumen and polymer, enhancing mill efficiency.
- Liquid additives are supplied via self-priming, gear-type, and dosing pumps, with percentage adjustments controlled from the central panel.
- Electro-pneumatic valves and optional compressor enable the unit to operate independently of external compressed air sources.
- Bitumen pipelines, pumps, mill, and intermediate tank are heated with thermal oil, ensuring gentle and efficient heating.
SPECIFICATIONS
Parameter
UOM
Value
Capacity
m3/h
8… 12
Amount of polymer
%
1… 5
Amount of plasticizer per 1m³ of bitumen
kg
0…100
Amount of adhesion additive per 1 m³ of bitumen
kg
0…10
Operation mode
continuous
Required power
-mill, kW 75
-overall, kW 110
Electric current
-voltage, V customizable
-alternating current (AC) frequency, Hz customizable
Dimensions, not more than:
-length, mm
5,400
-width, mm
1,620
– height (operating position), mm
2,650
Weight, not more than, kg
3,500