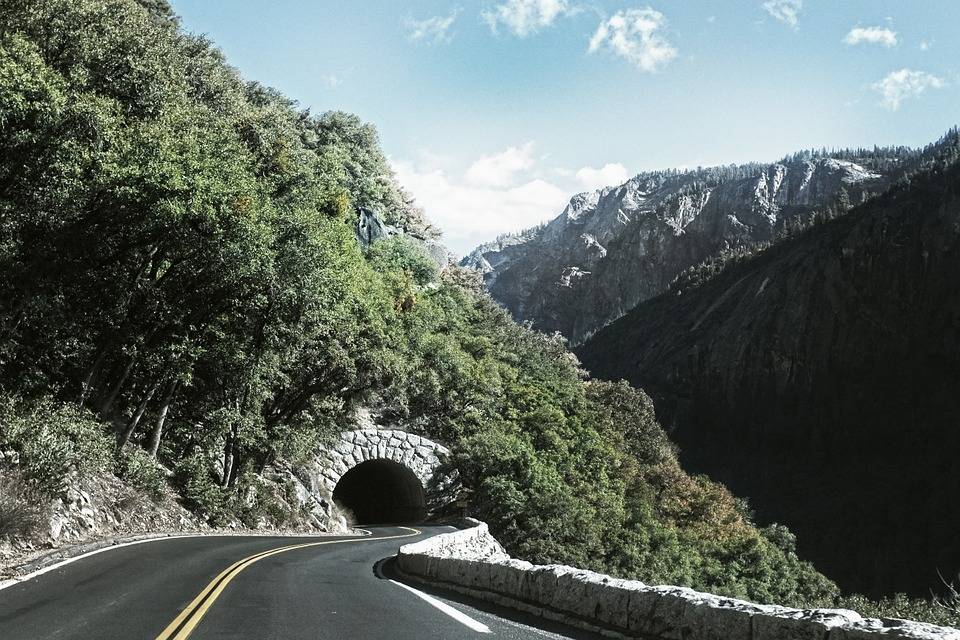
Construction of new facilities and installations requires quality materials. It is one of the requirements for obtaining durable structures serving humanity with good faith and fidelity for years.
But the reality is that not all construction materials fully comply with these requirements. This especially concerns road construction. The total length of roads in the world is about 64,285,000 km (as of 2013). The development of many countries is also accompanied by improvement of transport infrastructure and, as a consequence, construction of new roads. Therefore, this figure is constantly growing.
Due to the increase in traffic and harsh climatic conditions, traditional binders used in asphalt mixtures no longer provide the necessary durability of roads. In many cases, the durability is two to three times less than standard norm, causing additional costs to perform unscheduled, unbudgeted repairs.
It is much cheaper to use a high-quality material from the start to guarantee endurance. Over the past decade there have been many studies aimed at improving the quality of road surfaces. As a result, it was concluded that it is not necessary to abandon traditional bitumen, but it is necessary to adjust its characteristics by introducing special additives – modifiers. They give future road surface all the characteristics it is so lacking now. In particular: fracture and frost resistance, fatigue endurance, strength, etc. The main advantage of modified bitumen is extending the range of road operation temperatures. Various polymers are used in road construction. The most widely used are sulfur, rubber and crumb rubber.
Modified bitumen quickly proved its competitiveness; it also started to be used in other industries for roofing and waterproofing.
Existing methods for bitumen polymer modification are based on maintaining a high temperature (150-200ºS) and vigorous stirring of components.
When heated, bitumen softens and thermoplastic polymers become viscous fluids. Therefore, the process of mixing bitumen with polymers at high temperatures typically occurs in two stages: the emulsification of softened polymer in liquid bitumen and its subsequent partial or complete dissolution. The nature of polymer dispersion depends on its chemical nature and molecular weight, chemical composition of bitumen and their mixing ratio.