Colloid mill CLM-2/4
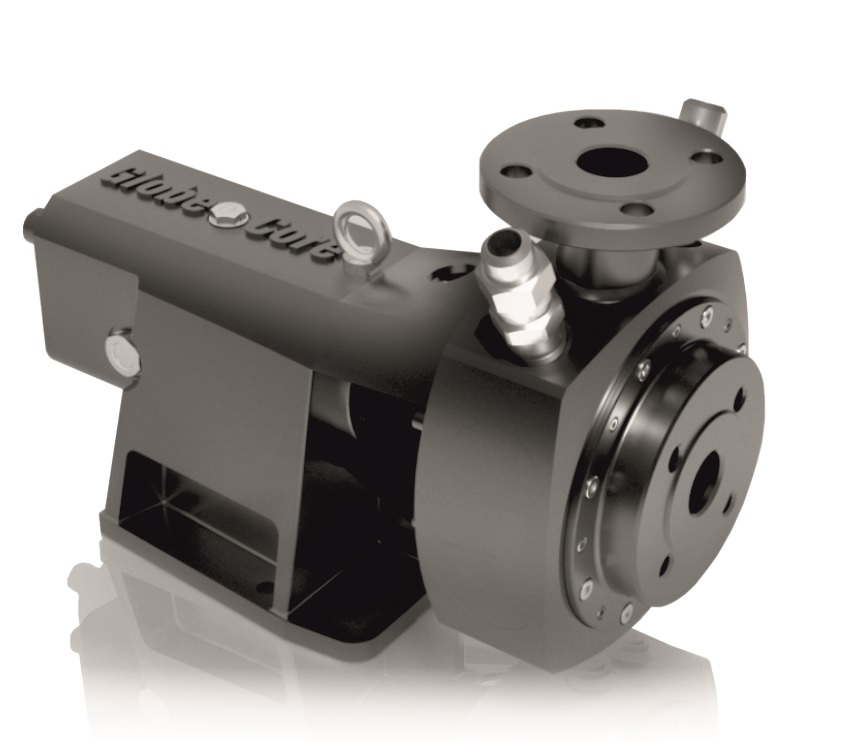
The CLM-2/4 colloid mill is engineered for inline homogenization and emulsification of liquid products, specifically designed to handle thick slurries subjected to high shear stresses, with a primary focus on preparing bitumen emulsions.
While its core function revolves around bitumen emulsion production, this versatile mill finds acceptance across various industries for the preparation, dissolution, and processing of a wide array of products.
Operational Principle
The operation of the CLM-2/4 colloid mill hinges on a rotor/stator system configuration. Within this setup, both the rotor and stator comprise concentric tool rings, featuring specialized configurations of grooves and holes aimed at optimizing the mechanical impact on the processed product.
During operation, the tool rings of the rotor (the moving component) and the stator (stationary component) align coaxially and rotate contact-free at a high relative speed, reaching up to 45 m/s. This contact-free rotation is maintained through precise axial and radial gaps engineered for technological purposes.
The processed product enters the mill’s operating chamber through the axial bore of the stator, serving as the product inlet. It then traverses through the rotor/stator system and is discharged radially through the product outlet.
As the product passes through the rotor/stator system, it undergoes intricate hydrodynamic processes characterized by variations in shear stresses, shear forces, and flow velocity. These conditions accelerate chemical reactions by increasing the contact surfaces of chemical agents, facilitating intensive dispersion, emulsification, homogenization, grinding, and pulverization of the processed product.
SPECIFICATIONS
№ | Parameter |
Value |
1 | Unit capacity, m3/h (gpm) |
2…4 (8.8… 17.6)* |
3 | Operating temperature, °С (°F), not more than |
150 (302) |
4 | Maximum pressure, bar (psi), not more than |
10 (145) |
5 | Product operating volume, L |
flow |
6 | Shaft seal type |
packing |
7 | Rotor/stator tooling type |
nozzle |
8 | Replaceable knife kit |
optional |
9 | Knife axial gap (preset), mm |
0.5…1.5 (2·10-2…6·10-2 ) |
10 | Knife radial gap, mm (in) |
0.25 (10-3) |
11 | Knife tip speed, m/s (mph), not more than |
45 (100) |
12 | Mill shaft and bearing rotation speed, rpm |
6,350 |
13 | Electric motor shaft rotation speed, rpm |
2,900 |
14 | Drive power, kW |
11 |
15 | Power voltage, V |
custom |
16 | Dimensions, mm (in), not more than: | |
-length |
900 (35) |
|
– width |
580 (23) |
|
-height |
450 (18) |
|
17 | Weight, not more than, kg (lb) |
190 (420) |
* – depending on the product (liquid).
ADVANTAGES
- The mill finds applications across various industries.
- It can be equipped with rotor/stator tooling of different types: nozzle, chamber, cone (for milling), and cone (for viscous products).
- Depending on the required intensity of mechanical and thermal product processing, the type of rotor/stator tooling and the number of operating stages (rings) are selected.
- The tools can be collapsible or made from a solid workpiece and various grades of steel, tailored to the intended purpose.
- Optimal tool geometry and material can be chosen to match the task at hand.
- The mill is suitable for operation both indoors and in sheltered outdoor spaces.