The acceptance of our quotation implies the acceptance of the following terms and conditions. Modifications of or deviations from them must be agreed in writing.
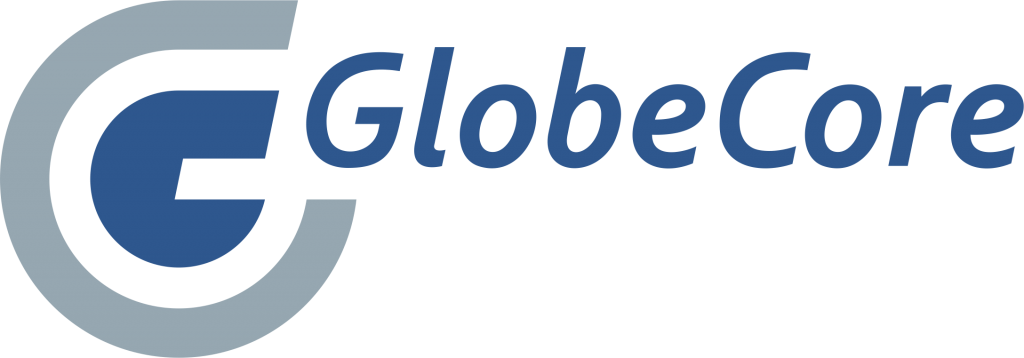
1. VALIDITY
Unless previously withdrawn, our quotation is open for acceptance within the period stated therein, or when no period is stated within ninety days only from the date thereof. Any order or orders arising from this quotation shall be subject to our confirmation in writing or by facsimile.
2. DOCUMENTS
Except where intended to serve as instructions for use or advertising, information in relation to our products and their operation remains our property and may without our consent not be utilized or copied, reproduced, transmitted or communicated to a third party. Illustrations, catalogues, colours, drawings, dimensions, statements of weight and measurements etc. made available by us as printed information are only meant to present a general idea of the goods to which they refer: they are approximate only and therefore not binding on us.
3. TRADE TERMS
Unless otherwise agreed, the Incoterms 2000 issued by the International Chamber of Commerce shall apply to the trade terms mentioned in our quotation.
4. DESPATCH
Full forwarding instructions must be sent with the order. The times given for dispatch are estimated and not binding; they have to be reckoned from the date of our written confirmation of the order or, where a Letter of Credit has been asked for, from the date of the bank’s advice that it has been opened, and, if agreed, confirmed, in conformity with our requirements. We reserve the right to dispatch the ordered goods as and when they are ready for dispatch; the goods may be sent in partial shipments. Unless otherwise agreed, the goods shall remain our property until paid for in full.
5. FORCE MAJEURE
In the event of the occurrence of force majeure we shall be entitled to suspend delivery of the goods for the duration of the prevention or delay caused by such force majeure, without being held responsible for any damage resulting there from to the purchaser. In that case the times given for delivery and the rendering of services shall be extended for the period of prevention or delay caused by such force majeure.
In the event of the period of prevention or delay caused by force majeure having lasted for a period exceeding twelve consecutive months, then and in that case we shall be entitled to cancel the order to the extent not yet executed without being liable to any indemnity whatsoever towards the purchaser. The expression “force majeure” shall mean and include any happening or event beyond our reasonable control – whether foreseeable or not at the time of our order confirmation – in consequence of which we cannot reasonably be required to execute our obligations.
Such circumstances include but are not restricted to: acts of God, war (whether declared or not), civil war, insurrection, seizure, fires, floods, strikes, epidemics, governmental regulations, embargoes, non-availability of any permits and/or licenses and/or authorizations required and defaults of our suppliers or sub-contractors caused by any such circumstances referred to in this Clause.
6. PAYMENT
Any payment to us will constitute a valid discharge only in so far as a bank account payable on first demand is credited in our favour for the amount concerned, irrevocably and free of charge, in the agreed currency and in any case in freely convertible and transferable funds.
7. LETTER OF CREDIT
Any Letter of Credit established in our favour shall be opened and confirmed by banks, which have adopted the Uniform Customs and Practice for Documentary Credits issued by the International Chamber of Commerce.
8. TESTS
Our goods are carefully inspected and, where practicable submitted to standard tests at the factories before dispatch. If special tests in the presence of the purchaser or his representative are required, these must be specified by the purchaser when giving the order and shall, unless otherwise agreed, be made before dispatch; all costs connected with such tests will be charged extra. In the event of any delay on the part of purchaser in attending such tests after fourteen days notice that the goods are ready to be tested, the tests will proceed in the purchaser’s absence and shall be deemed to have been made in his presence.
9. INSTALLATION
Unless expressly stated otherwise, the installation of the goods supplied by us is not included in our quotation.
10. GUARANTEE
We guarantee to the purchaser the good quality of the goods supplied for the period of one year against all defects or failures which appear therein under proper use and maintenance, and arise solely from faulty materials or workmanship, it being understood that:
(a) Such guarantee does not cover damage sustained by normal wear and tear or any damage arising in consequence of negligence or improper manipulation of the goods or parts thereof, or of improper storage in the event of the goods wholly or partly being stored by the purchaser previous to installation, use or resale to ultimate buyers;
(b) Such guarantee shall not include separate deliveries of spare parts and components to which a specific manufacturer’s guarantee applies.
Our liability under this guarantee shall be to supply to the purchaser, free of charge, replacements of such parts as have proved to have such defects as set out here above, provided BiodieselMach is informed through E-mail or by facsimile within fourteen days after the defects have revealed; the defective parts shall become our property as soon as they have been replaced.
Compliance with our guarantee undertaking mentioned above or with any agreed modification thereof shall be considered to give full satisfaction to the purchaser; any claim of the purchaser for compensation or for dissolution of the contract shall be excluded.
11. LIABILITY
We shall not be liable for any consequential or other damage nor for any loss of whatsoever nature and howsoever arising other than those for which we have expressly assumed liability herein.
The United Nations Treaty, adopted in the framework of UNCITRAL on April 11, 1980 in Vienna regarding Contracts for the International Sale of Goods [C.I.S.G.] shall not apply.