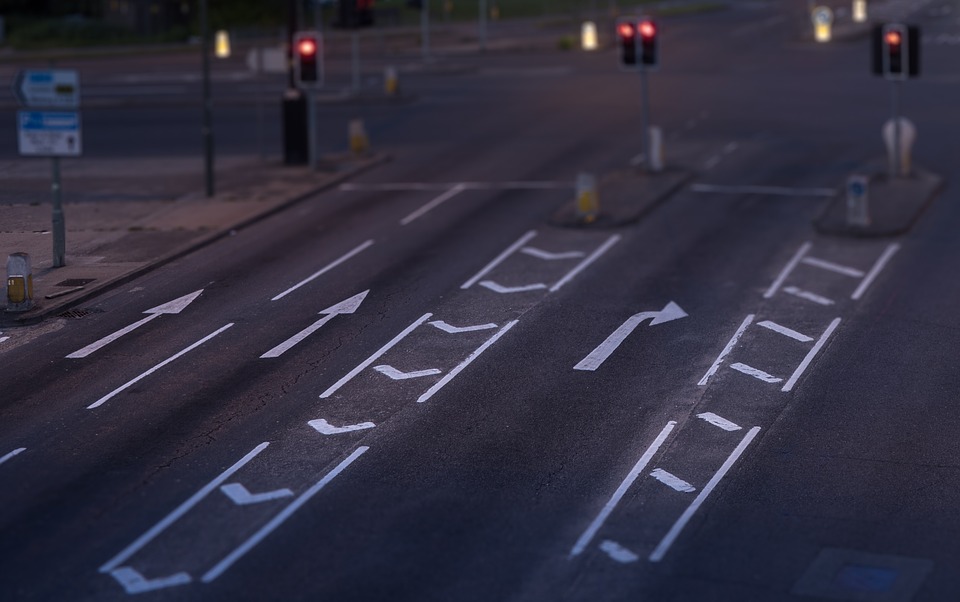
Bitumen properties. Petroleum bitumen is widely used in construction. It is due to the versatility of this binding material. And it is successfully used in road works, roofing, waterproofing, sealing, for protection of pipelines, canals etc.
But when used in cold weather conditionsб bitumen becomes brittle, which leads to the rapid failure of bitumen coating. This leads to excess expenditure of bituminous materials. Also, bitumen aging is intensified by sunlight and temperature fluctuations.
The solution is the introduction of additives that can improve the performance properties of road bitumen. For example, adding rubber into bitumen reduces brittleness while increasing temperature and heat resistance. The use of polymers for bitumen modification improves the durability of pavement. These conclusions were made by a long-term observation of the road surfaces dressed with modified bitumen. Also, modifications improve bitumen resistance to deformation at low and high temperatures, water resistance, durability and other characteristics.
First, the use of polymer additives to improve the properties of bitumen was explained by chemical bonds between bitumen and polymers. But the infrared analysis showed the absence of new bonds in bitumen-polymer compositions.
The electron microscopic analysis and optical analysis showed the particle distribution of bitumen and polymer. It was noted that a small portion of polymer (1-2%) dissolves in bitumen oils with low molecular weight. Adding 5-10% of polymer increases particle size due to aggregation, 10-15% of polymer produces a cross-linked structure. When the polymer content exceeds 25%, the bitumen enters the polymer cell structure.
In addition to polymer additives, bitumen cracking resistance is improved by adding oil or oligomers, also called plasticizers, which enhance bitumen properties at low temperatures.